How to Schedule Preventive Maintenance Servicing for Maximum Efficiency
Best Practices for Maintenance Planning
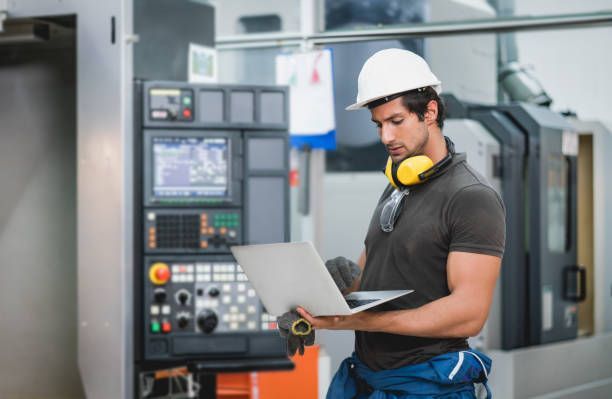
Preventive maintenance servicing keeps machinery, equipment, and infrastructure in top condition. A properly organized maintenance approach enables organizations to prevent sudden equipment failures, minimize operational shutdowns, and decrease repair expenses. The effectiveness of maintenance scheduling determines both the best possible efficiency results and the least amount of operational interruptions.
During this blog, we will examine proven methods to plan preventive maintenance servicing that maintains asset operation at peak levels alongside maximum productivity.
What Is Preventive Maintenance Servicing?
Routine inspections, combined with preventive repairs and scheduled checks, need to be performed prior to equipment failure during preventive maintenance servicing. Businesses choose planned upkeep strategies in advance to preserve both equipment functional reliability and the operational performance level of their machines.
Establishing a preventive maintenance structure helps companies avoid critical equipment breakdowns while achieving a longer equipment lifetime, together with increased efficiency. Businesses that collaborate with dependable preventive maintenance companies benefit from access to proficient and dependable service operations.
Steps to Schedule Preventive Maintenance for Maximum Efficiency
1. Assess All Equipment and Assets
Before scheduling maintenance, evaluate all equipment and assets that require servicing. Identify:
- Critical equipment that directly affects operations.
- Machinery with frequent breakdowns or past maintenance issues.
- Maintenance of assets must follow the guidelines established by their manufacturers.
The assessment aids you in establishing priority rankings for equipment that requires regular preventive maintenance service.
2. Categorize Equipment by Maintenance Needs
Every piece of equipment requiring maintenance should be positioned according to its scheduled service frequency. Three scheduling approaches are available for your use:
- Time-based maintenance: Regular servicing intervals should exist at the levels of weekly, monthly, or annually.
- Usage-based maintenance: The maintenance schedule depends on both the number of operational hours and manufacturing cycle lengths.
- Condition-based maintenance: Your system should use sensors and data analysis tools to identify proper servicing intervals.
You will maximize efficiency and cut down on avoidable maintenance costs through method integration.
3. Create a Maintenance Calendar
A structured maintenance calendar ensures that you don’t overlook any servicing tasks. Include details such as:
- The specific equipment scheduled for servicing
- The type of maintenance required (inspection, lubrication, calibration, part replacement, etc.)
- The assigned personnel responsible for the task
Implementation of maintenance management software tracks schedules for better plan organization and automates reminder systems while effectively handling servicing activities.
4. Hire a Reliable Preventive Maintenance Company
Maintenance teams operated by an organization handle day-to-day upkeep, yet utilizing professional preventive maintenance companies provides advanced service quality. A reputable provider like KBC Service provides experts and specific tools along with tailored maintenance solutions that follow industrial standards.
Your search for a maintenance provider should focus on their experience level, combined with their service capabilities and speed, as well as their customer feedback. Choosing the right partner maintains smooth operations and reduces service disruptions.
5. Schedule Maintenance During Non-Peak Hours
Maintenance at bad times will create interruptions to your business operations. The scheduling of preventive maintenance service needs to occur at times when equipment usage is minimal. Consider:
- Scheduling maintenance after business hours or on weekends.
- Conducting maintenance in phases instead of shutting down all operations at once.
- Aligning seasonal maintenance with off-peak business cycles.
The strategic timing of maintenance will help your operations stay productive and maintain equipment quality at its peak levels.
6. Use Predictive Maintenance Technology
Modern technology allows businesses to enhance preventive maintenance with predictive techniques. Sensors and IoT devices track real-time performance data and identify early signs of wear or malfunction.
Such integration enables you to achieve the following benefits:
- Detect potential problems before they escalate.
- Reduce unnecessary maintenance on well-functioning equipment.
- Adjust servicing schedules based on actual equipment conditions.
These strategies help optimize efficiency while minimizing maintenance costs.
7. Keep Accurate Maintenance Records
Routine documentation makes it possible to monitor equipment performance, which then leads to enhanced servicing schedule optimization. Keep records of:
- The maintenance date and type of servicing performed
- Parts that were replaced or repaired
- Equipment performance before and after servicing
- The next scheduled maintenance date
These records allow you to detect recurring equipment problems while helping you determine proper servicing durations, which results in better future reliability.
8. Train Employees on Basic Maintenance
The essential need for professional servicing improves when you train employees to handle fundamental upkeep tasks, which enables them to stop small problems from developing into extensive issues. Teach staff how to:
- Perform regular cleaning and lubrication
- Conduct visual inspections for early signs of damage
- Handle and operate equipment properly to avoid unnecessary wear
When employees actively participate in maintenance efforts, they contribute to the longevity and efficiency of equipment.
9. Allocate a Maintenance Budget
Businesses must initially invest in preventive maintenance because they will avoid needing expensive emergency repairs later. Reserving an allocated budget allows you to sustain continuous servicing without causing monetary difficulties. The collaboration with KBC Service allows businesses to develop cost-efficient servicing plans according to their requirements.
10. Regularly Evaluate and Adjust the Maintenance Plan
Adjust the maintenance plan based on operational data and field feedback. Adjust the maintenance plan based on operational data and field feedback. Maintenance inspection schedules should occur when specific equipment demonstrates more rapid wear. Equipment upgrade or servicing technique modification should be considered as an intervention if maintenance interventions do not decrease equipment downtime levels. You may optimize the effectiveness of your preventative maintenance plan by conducting routine evaluations.
The Benefits of an Effective Preventive Maintenance Schedule
A well-organized preventive maintenance plan delivers several long-term advantages:
- Extended Equipment Lifespan: Effective maintenance prevents wear and tear from continued use.
- Reduced Downtime: Regularly scheduled maintenance helps maintain operational normality in business.
- Lower Repair Costs: Searching for small issues at their beginning point saves money from needing expensive restorations.
- Enhanced Workplace Safety: Well-maintained equipment reduces accident risks.
- Improved Energy Efficiency: Well-optimized equipment requires less energy, thus reducing utility costs.
Why Trust KBC Service for Preventive Maintenance Servicing?
Choosing a trustworthy maintenance provider determines the success level of your preventive maintenance strategy. The professional repair solutions at KBC Service meet specific needs within your sector. Implanting skilled experts who utilize premium tools and operate with organizational efficiency keeps your equipment operating at peak performance levels.
Conclusion
Correct scheduled preventive maintenance services stand as the fundamental key to achieving high operational efficiency and minimizing equipment downtime expenses. Operational reliability improves when businesses conduct equipment need evaluations along with scheduled maintenance through predictive methods and by collaborating with trusted organizations such as KBC Service.
Businesses that invest in preventive maintenance for today will achieve both long-term cost savings and increased production rates and elongated equipment operational life. The preventive maintenance solutions you need are available at KBC Service through their business-specific servicing plan development service.