How to Avoid Common Welding Defects in Heavy Machinery
Essential Welding Techniques for Heavy Machinery
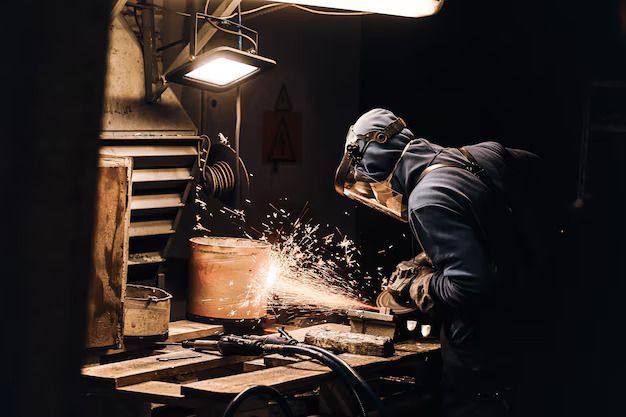
Heavy machinery construction and maintenance require welding. Anything from a construction crane or an excavator to an industrial cardboard baler depends on strong and accurate welds for longevity and effectiveness. However, it opens doors for welding defects that can jeopardize the load-carrying capacity of any structure installed in heavy machinery.
With a sound understanding of the common defects in heavy machinery welding and their effective solutions, they would be set to visit Machining and Welding for Heavy Machinery. This guide will walk through how such criteria would be determined by frequent welding problems and proven combat strategies against them.
1. Understanding Common Welding Defects
Various welding defects emerge from a combination of insufficient technical skill, wrong material preparation, and sub-optimal welding parameter settings. The main welding defects found in heavy machinery welding include:
- Porosity – The weld area contains small holes that result from trapped gases.
- Cracking – fractures appear within welds and their adjacent heat-affected zone when stress levels become too high or improper cooling takes place.
- Undercut – A groove at the weld toe that weakens the joint.
- Incomplete Fusion – Failure of the weld metal to fuse properly with the base metal.
- Slag Inclusions – The weld becomes weaker because non-metallic particles remain trapped inside it.
- Distortion – The excessive heat produced from welding operations leads to metal distortion.
Every defect in industrial cardboard balers, along with heavy equipment systems, has the potential to reduce equipment reliability. These welding issues can be stopped through correct best practices usage.
2. Preventing Porosity in Welds
The entry of gases, including hydrogen or oxygen, within the weld pool creates porosity, which represents a common welding problem. Weak, vulnerable welds are created through the trapping of gases inside the weld pool, which makes the welds potentially fail during stress situations.
How to Prevent Porosity:
- The surface should be completely free of moisture, along with rust and oil, at the time of welding.
- Select the suitable shielding gas type while managing gas flow correctly.
- Careful control of arc length is necessary because it prevents atmospheric contaminations in the weld.
- Both storage containers should remain dry to avoid moisture absorption by their contents.
Proper preventative measures enable you to manufacture welds that extend the operational lifespan of KBC Service heavy equipment.
3. Preventing Cracking in Heavy Machinery Welding
Structural failure becomes a risk whenever proper defect repair is not executed for cracking, which is a major welding problem. The occurrence of this defect can start right away after welding or it may develop gradually as a result of material stress.
How to Prevent Cracking:
- Metals should reach initial heat before welding to lower the contrast in temperature.
- Select filler material that provides equivalent strength, along with flexibility, to the base metal material.
- Managing the cooling process will stop hardness from building up in the heat-affected region.
- Designing joints correctly, along with structured weld sequencing methods, can help reduce welding-induced stress.
Heavy machinery needs to prevent cracks across its operation because extreme conditions make the use of preventive measures essential for maintaining performance and safety levels.
4. Preventing Undercut Defects
A weakened weld occurs through undercuts because they form grooves at the weld toe area, increasing joint failure risk when subjected to loads. The correct welding techniques prevent this problem from occurring.
How to Prevent Undercut:
- Use proper electrode angles to avoid excessive melting at the edges.
- Maintain the correct welding speed to prevent overheating.
- Reduce amperage when needed to avoid burning into the base metal.
- For thick materials subject to joining, the artisan must execute multiple heat application runs until heat distribution becomes uniform.
By eliminating undercuts, you can ensure stronger and more durable welds in industrial cardboard balers and other heavy machinery.
5. Ensuring Complete Fusion in Welds
Structural weaknesses form when the weld metal fails to properly bond with the base material.
How to Prevent Incomplete Fusion:
- Maintaining precise heat settings will lead to complete penetration of the material.
- Place the electrode in the correct position so it touches the base metal properly.
- A thorough cleaning should remove all coatings, together with oxides and contaminants, from the base metal surface.
- The welding method must enable pass fusion to occur naturally.
KBC Service requires complete weld fusion to make reliable top-quality industrial machinery.
6. Avoiding Slag Inclusions
When non-metallic material gets lodged inside a weld joint, it forms slag inclusions, which weaken both the strength and endurance of the weld.
How to Prevent Slag Inclusions:
- Weld with the correct angles and method to allow impurities to float toward the weld surface.
- Welding operations should include the removal of accumulated slag between each welding pass.
- The proper choice of flux and electrode, combined, will help reduce the amount of slag formation.
- Sustaining an even arc distance will help manage the movement of slag material.
Extensive and proper slag removal techniques enable welds to stay free from defects and thus extend the lifespan of welded heavy machinery projects.
7. Preventing Distortion in Heavy Machinery Components
The warping of metals brought on by excessive heating is referred to as distortion, and it can impair part alignment and operation.
How to Prevent Distortion:
- Use a controlled welding sequence to distribute heat evenly.
- Clamp and fixture the workpiece to maintain alignment.
- Use backstep welding or skip welding techniques to minimize heat concentration.
- Internal stresses can be minimized by allowing components to cool in a controlled manner.
The equipment will operate correctly and without misalignment if the welding structures are properly maintained.
8. The Importance of Proper Training and Inspection
If the welder is not properly trained, welding flaws may still happen even with the best methods and tools. Defect prevention requires routine inspection and quality control procedures.
Best Practices for Training and Inspection:
- Provide continuous training to welders to enhance their skills.
- Carry out visual checks for early detection of defects.
- Utilize NDT techniques such as ultrasonic testing or radiographic testing.
- Ensure adherence to welding codes and standards.
KBC Service's commitment is to prioritize highly skilled welding professionals and engage in continuous quality checks to preserve the best standards in the fabrication of heavy machinery.
Conclusion
Welding defect prevention on heavy machinery entails a blend of proper techniques, material tests, and quality inspections throughout fabrication. The avoidance of porosity, cracking, incomplete fusion, and distortion ensures strong, reliable welds on any machinery, from the industrial cardboard baler to any apparatus in between. Following established protocols for best welding practices will ensure extended lifetime and improved performance.
KBC Service offers the best individualized welding services to meet your heavy machinery needs and specifications.
To ensure that your equipment lasts a long time and keeps functioning properly, get in touch with us.